The gas spring lifetime testing method involves assessing various performance metrics of gas springs under simulated operating conditions to determine their durability and functionality. Below is a comprehensive explanation of the method, including additional details regarding product performance and technical specifications.
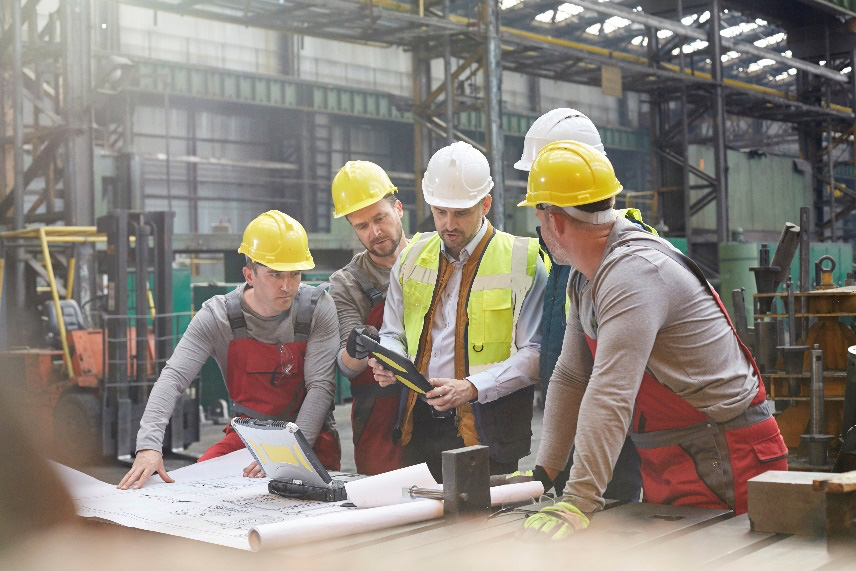
1. Test Setup and Initial Measurements
The gas spring is mounted vertically on a fatigue testing machine, with the piston rod oriented downwards. Both ends of the gas spring are connected using its mounting heads. The first test cycle records the opening force and activation force. In the second cycle, the test measures the extension force and compression force, denoted as F1, F2, F3, and F4, respectively.
Using these measurements, key performance indicators such as the nominal force, dynamic friction force, and the force ratio of the gas spring are calculated. These parameters provide insight into the gas spring’s ability to operate effectively under load.
2. Rigid-Locking Gas Springs
For gas springs with rigid locking mechanisms, the piston rod is extended to its full length, and the locking force is measured while in the fully extended position. The testing machine operates at a speed of 2 mm/min. The axial compression force required to produce a 1 mm displacement of the piston rod is taken as the locking force. This metric is critical for ensuring that the gas spring maintains rigidity under load without slippage.
3. Elastic-Locking Gas Springs
For elastic-locking gas springs, the unit undergoes three preliminary cycles under simulated operating conditions. After these cycles, the piston rod is locked at the midpoint of its stroke. The testing machine measures the locking force with a displacement speed of 8 mm/min. The axial compression force required to displace the piston rod by 4 mm is recorded as the locking force. This process simulates the real-world application of the spring, ensuring it locks securely at various points during its operation.
4. Gas Spring Lifetime Test Procedure
Gas springs that have undergone high and low-temperature storage performance tests are subjected to a lifetime cycle test. The spring is clamped onto the gas spring lifetime testing machine, which simulates real-world operating conditions. The testing machine operates at a cycle frequency of 10-16 cycles per minute, and the cylinder temperature of the gas spring must not exceed 50°C during the entire testing process.
After every 10,000 cycles, the performance of the gas spring is measured to verify if it still meets the required force characteristics. Upon completion of 30,000 cycles, the gas spring must meet the following performance criteria:
- A. Sealing Performance: The gas spring’s control valve must maintain a proper seal when closed. This ensures that the piston rod remains locked at any position, preventing unintended movement.
- B. Cycle Life: After the high and low-temperature storage performance tests, the gas spring must withstand 30,000 operational cycles without significant degradation. The nominal force should not decrease by more than 10% by the end of the test.
5. Test Considerations and Additional Metrics
- Temperature Control: Maintaining the cylinder temperature below 50°C during testing ensures that thermal expansion does not affect the performance of the gas spring, providing a more accurate assessment of its durability.
- Force Degradation: Continuous force measurement during the testing process helps monitor how the gas spring’s force characteristics evolve over time. This data is crucial for determining the spring’s long-term reliability in dynamic applications.
The gas spring lifetime testing method is a crucial tool for evaluating the reliability and durability of gas springs. By simulating real-world conditions, this method ensures that gas springs maintain optimal performance over extended use, particularly in environments with temperature fluctuations. The data obtained from these tests provide manufacturers and engineers with valuable insights into the long-term functionality of their products, helping to guide improvements in design and materials.