The operation of a stainless steel gas spring is based on specific physical principles. When no external force is applied, the gas spring naturally extends to its maximum length, which is its minimum compressed state. At this point, the pressure on both sides of the piston is equal. However, due to the different surface areas on either side, a pressure differential is created, providing the supporting force of the gas spring.
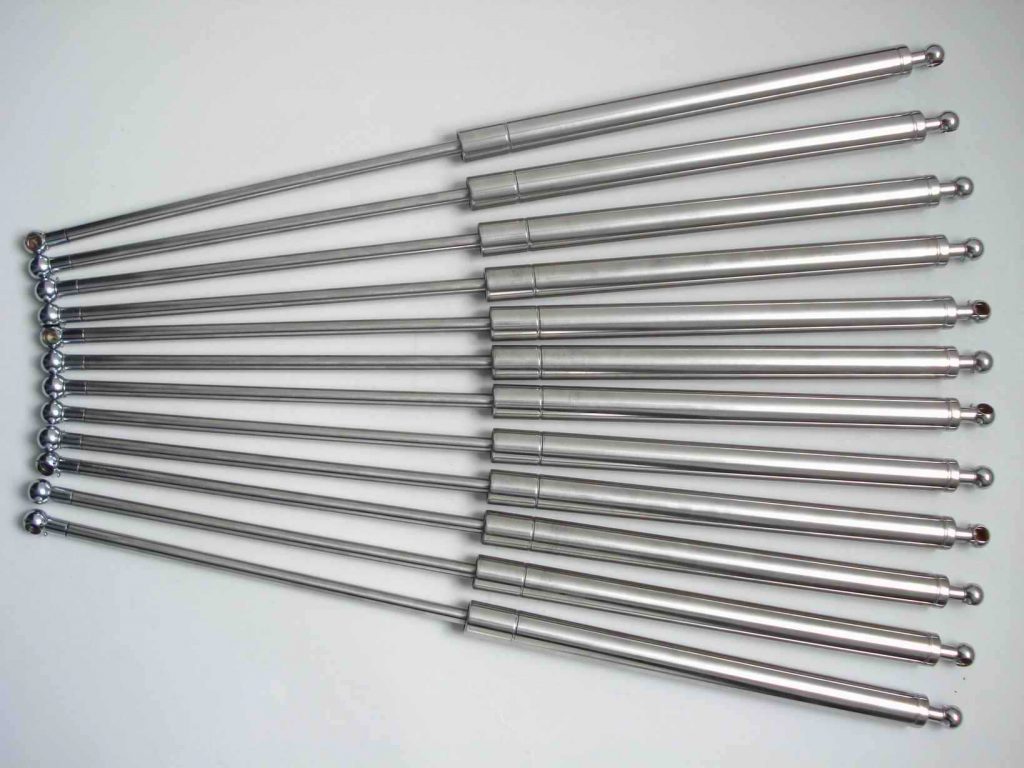
The total instantaneous supporting force provided by the gas spring during movement consists of two components:
- Supporting Force Generated by Pressure Difference: This occurs due to the difference in the effective areas of the piston sides.
- Frictional Force: The movement of the piston rod inside the gas chamber generates friction, which also contributes to the overall support.
When an external force compresses the gas spring, the volume inside the gas chamber decreases as the piston rod displaces the gas, leading to an increase in gas pressure. As a result, the supporting force generated by the pressure differential also increases.
Frictional Force Dynamics:
- The higher the pressure inside the gas chamber, the greater the frictional force.
- The faster the piston rod moves, the greater the frictional force.
- The further the piston rod is from its natural extended position, the greater the frictional force.
Temperature Impact:
Temperature plays a significant role in the gas spring’s performance. As the ambient temperature decreases, the pressure inside the gas chamber decreases, leading to a reduction in the supporting force provided by the gas spring.
In summary, the performance of stainless steel gas springs is influenced by both internal pressure dynamics and external factors such as friction and temperature. These factors determine the overall support that the gas spring can provide in various applications.