In recent years, mold technology and manufacturing techniques have significantly advanced, driving the mold industry toward precision, efficiency, and extended product lifespan. Traditional elastic components used in molds, such as gas springs and rubber elements, have certain limitations during operation. For instance, gas springs and rubber components must be preloaded and can only deform up to a specific limit, making them difficult to compress further. Additionally, the pressure curves provided by these components often fail to meet the requirements of various stamping processes, leading to a decline in the quality and pass rate of stamped products. While air cushions offer a partial solution, using press machine air cushions poses challenges, such as inconvenient mold design, adjustment, and usage. Furthermore, the forces exerted by air cushions can be inaccurate and take up considerable space. As a result, there has been a demand for the development of new elastic components that can replace conventional elastic elements.
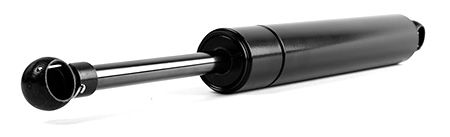
What is a Controllable Gas Spring?
A controllable gas spring is a modern elastic component that seals high-pressure gas within a designated container. When an external force is applied via a piston rod, the gas is compressed. Once the force is removed, the high-pressure gas within the spring restores the system, providing a specific amount of elastic force. Compared to traditional elastic components, the controllable gas spring offers several unique advantages that make it ideal for use in modern mold-making and other industrial applications.
Key Advantages of Controllable Gas Springs:
High Initial Force in a Compact Space: Unlike conventional elastic components, controllable gas springs do not require preloading to generate substantial initial force. This makes them highly effective in applications where space is limited but strong elastic forces are needed.
Constant or Adjustable Pressure: One of the most significant advantages of a controllable gas spring is its ability to maintain a nearly constant pressure throughout its operational cycle. This ensures stable and reliable performance during prolonged use. Additionally, the pressure force and the point of application can be adjusted over time, allowing for real-time customization to suit different operational needs.
Simplified Mold Design and Manufacturing: The controllable gas spring simplifies mold structure, making mold design more straightforward and shortening the mold-making process. This improvement in design efficiency helps reduce production lead times while ensuring high-quality stamped products, ultimately increasing overall production efficiency.
Enhanced Safety and Reliability: Controllable gas springs are designed with safety and longevity in mind. Their construction ensures reliable operation over extended periods, reducing the need for frequent replacements or maintenance. Furthermore, they are easy to install and service, contributing to lower long-term operational costs.
Versatility in Industrial Applications: The adjustability of force and pressure makes controllable gas springs suitable for a wide range of industrial processes, including those that require precise force control and flexibility. They can be used across various sectors such as automotive manufacturing, aerospace, heavy machinery, and consumer goods, where high precision and reliability are crucial.
Technical Features:
Pressure Regulation: The ability to control and maintain the internal gas pressure means that the performance of the gas spring can be fine-tuned for specific applications. This precision control is critical in industries where exact force application is needed.
Durable Construction: These springs are typically constructed from robust materials that can withstand high pressure and provide long service life even under harsh working conditions.
Compact and Lightweight: Controllable gas springs are designed to be compact, making them ideal for use in space-constrained environments while still delivering a high level of performance.
Conclusion:
Controllable gas springs represent a significant advancement over traditional elastic components in terms of performance, flexibility, and ease of use. Their unique characteristics—such as high initial force, constant pressure, adjustability, and ease of integration—make them an excellent choice for modern industrial applications, particularly in mold design and manufacturing. By improving the precision and efficiency of stamping processes, controllable gas springs enhance product quality and operational reliability, providing a competitive edge in today’s fast-evolving industrial landscape.