Gas springs are widely used across various industries due to their versatile applications and functionality. The demand for gas springs has grown significantly as they are employed in everything from automotive components to industrial equipment. When selecting a gas spring, understanding key product features, materials, and performance characteristics is crucial to ensure longevity and efficiency in your specific application.
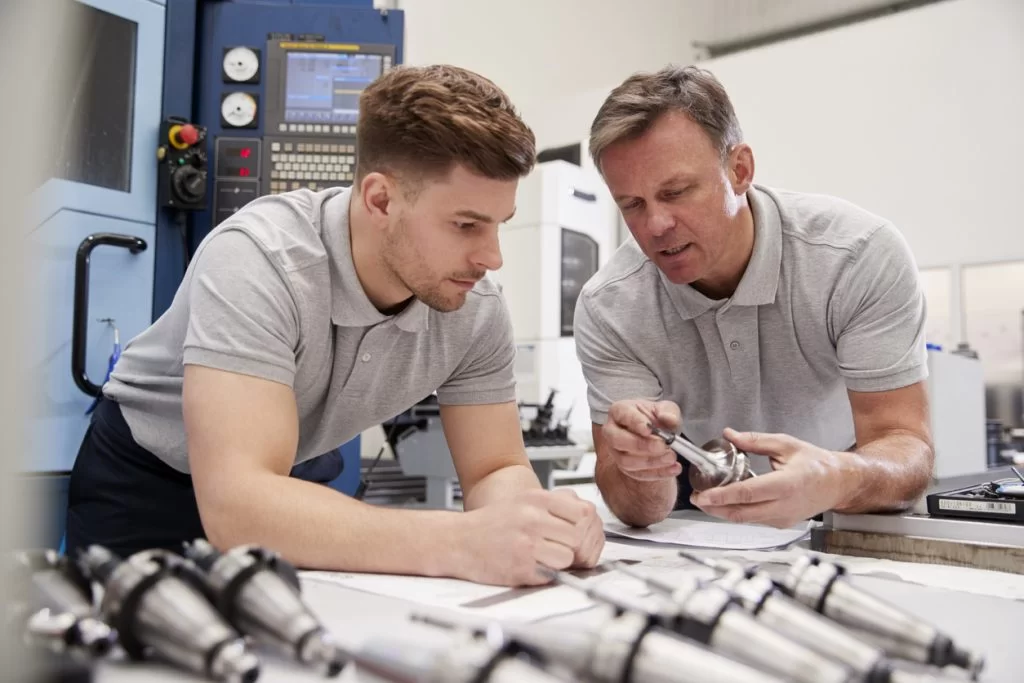
1. Material Selection
The materials used in gas springs play a pivotal role in their performance and durability. While the visible parts like the cylinder tube and support rod are important, the internal components, such as piston seals and gaskets, also determine the effectiveness and lifespan of the gas spring.
External Materials: The main external components, such as the cylinder and piston rod, are typically made of steel or stainless steel. Stainless steel gas springs are particularly recommended for environments exposed to high humidity or temperature fluctuations. These materials offer enhanced corrosion resistance, making them suitable for challenging conditions such as outdoor or marine applications.
Internal Components: The seals and gaskets within the gas spring ensure airtight sealing, preventing gas leakage. Inferior materials used in these internal components can cause gas leakage over time, leading to reduced pressure and a significant decline in performance. High-quality gas springs maintain their force over extended periods, even after hundreds of compression and extension cycles.
2. Pressure and Force Considerations
The gas pressure inside the spring is one of the most critical factors determining its force output. This pressure must be carefully adjusted to match the specific needs of the application.
Force Adjustment: The gas-filled cylinder exerts a force that needs to be tailored for each application. A gas spring with excessive force may make it difficult to close a lid or cover, while inadequate force can lead to inefficient opening and support. Precision in adjusting this force ensures optimal performance without compromising ease of use.
Application-Specific Adjustments: When choosing a gas spring, consider the desired balance between opening speed and ease of closure. For instance, increasing the gas pressure may cause a lid to open quickly, but it may also make it more challenging to close. Therefore, finding the right balance of gas pressure to suit the weight and function of the object being supported is essential for a smooth operation.
3. Protective and Maintenance Features
To maximize the lifespan of gas springs, certain protective measures and accessories are recommended. These additions not only enhance the durability of the gas spring but also ensure it continues to operate at peak efficiency.
Protective Tubes: Protective tubes shield the piston rod from damage, dirt, and moisture, which can degrade the performance of the gas spring. In environments with high dust or corrosive elements, these tubes are crucial in maintaining smooth and consistent operation.
Coatings and Paints: Applying protective coatings or paints on the external surface of the gas spring can prevent corrosion and wear, especially in outdoor or industrial settings. These coatings form a barrier against environmental factors such as moisture, salt, and chemicals, which could otherwise shorten the gas spring’s operational life.
Regular Maintenance: Periodic cleaning and inspection of the gas spring, especially in environments prone to contamination, can prevent premature failure. Simple maintenance routines, like wiping down the rod and cylinder or applying rust inhibitors, can significantly enhance the performance and lifespan of the gas spring.
4. Application Environments and Customization
Gas springs are highly customizable based on the specific requirements of their application. Environmental conditions such as temperature, humidity, and exposure to chemicals or other corrosive substances should be considered when selecting the material and design.
Temperature and Humidity Considerations: Gas springs designed for high-temperature environments need to be equipped with seals and materials that can withstand heat without losing effectiveness. Similarly, in cold climates, the gas spring’s performance must be tested to ensure it doesn’t lose force or become brittle.
Specialized Applications: For applications exposed to extreme conditions, such as marine or offshore industries, specialized gas springs made of highly resistant materials, such as stainless steel with additional protective coatings, are often required. These gas springs are designed to endure prolonged exposure to saltwater, high winds, and extreme pressure fluctuations.
Conclusion
Choosing the right gas spring involves more than simply picking a product off the shelf. Understanding the materials, force adjustments, protective features, and environmental factors can ensure that the gas spring performs optimally and has a long service life. Whether for industrial machinery, automotive components, or specialized equipment, proper gas spring selection ensures safety, durability, and functionality.
By considering these factors and investing in high-quality materials and protective measures, gas springs can reliably support your applications for years to come.