Controlled gas springs, also known as self-locking gas springs, are specialized gas springs that can lock in any position during their stroke. This key distinction, based on their operating principles, sets them apart from regular gas springs and grants them several significant advantages. Controlled gas springs have a relatively slower speed, exhibit minimal dynamic force variation (usually within a 1:1.2 range), and are easier to control. However, they also have some drawbacks, such as a larger size compared to coil springs, higher cost, and a relatively shorter lifespan.
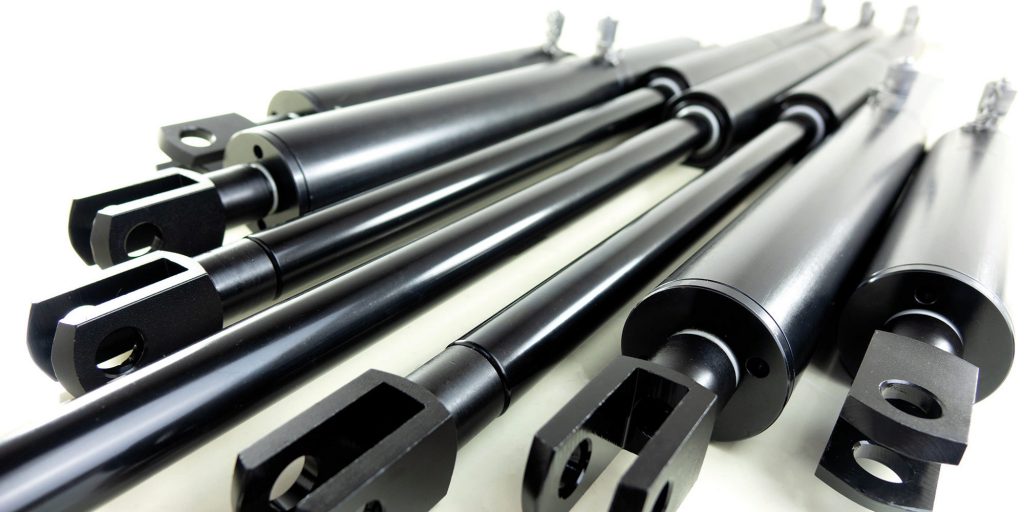
Unlike mechanical springs, gas springs feature an almost linear elastic curve. The elastic coefficient (X) of standard gas springs typically ranges between 1.2 and 1.4, with other parameters being adjustable based on specific requirements and working conditions. One key characteristic of controlled gas springs is that they require preloading to achieve the designed damping force. However, this damping force increases significantly as the stroke progresses, which may lead to instability and could hinder the proper forming of parts. This is particularly undesirable when dealing with tensile forces, as it may impact the quality of stamped components and complicate mold design, extending the time required for mold changes on the press.
The working principle of controlled gas springs involves filling a sealed pressure cylinder with inert gas or a gas-oil mixture. The internal pressure of the cylinder is several times, or even tens of times, higher than atmospheric pressure. The pressure difference is generated by making the cross-sectional area of the piston rod smaller than that of the piston, thereby driving the movement of the piston rod. The calculation method for gas springs combines the lever principle with the inverse proportionality theorem.
Gas springs are highly sealed products, and issues such as gas or oil leakage can be a sign of significant quality problems. When selecting a gas spring, it is important to assess the manufacturing quality, company scale, and research and development capabilities. For export or bulk purchases, conducting thorough testing of the gas spring is crucial. Ideally, the force of a gas spring should remain constant throughout the entire stroke. However, due to manufacturing factors, variations in force are common and serve as a key indicator of quality: the smaller the variation, the better the quality; larger variations indicate poor quality.
It is also important to note that gas springs are not designed to be recharged with gas by the user. If a gas spring exhibits leaks, it must be returned to a repair shop or the manufacturer for recharging. Leaking gas or oil typically indicates that the internal seals of the gas spring have failed. Common causes of gas spring defects include poor manufacturing quality, such as rough piston rods or inferior seals. Additionally, damage to the piston rod, such as pits, grooves, or sharp burrs, can tear the seals. Problems can also arise if the piston rod is contaminated with paint or adhesive.