Gas springs are widely used across various industries, including automotive, textile machinery, printing equipment, office devices, and engineering machinery. To ensure optimal performance and longevity of gas springs, it is critical to adhere to specific installation and operational guidelines. Below are the key working environment requirements and technical considerations for controllable gas springs:
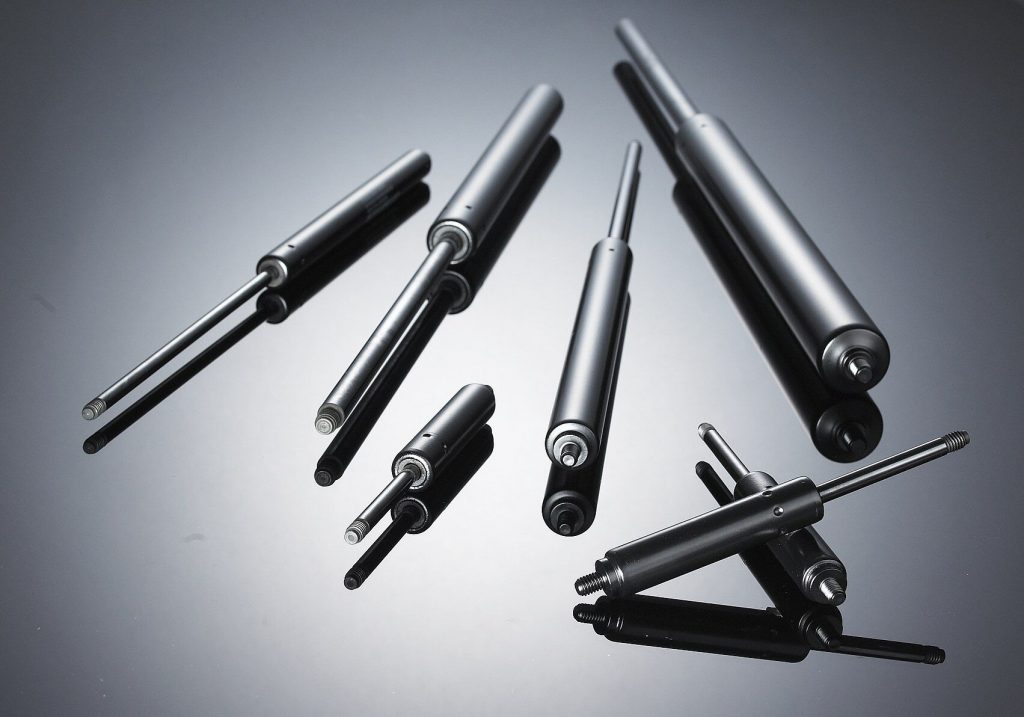
1. Correct Installation for Optimal Performance
Typically, hydraulic support rods differ in installation direction compared to gas springs. A proper installation ensures minimal friction during operation, which enhances the cushioning effect of the gas spring. To maximize efficiency, care must be taken to install the gas spring in alignment with the object’s structural design, reducing friction and wear over time.
2. Alignment of Installation Timing and Load Distribution
The installation of the first gas spring and the hydraulic support rod must be done in sequence, with special attention to the load distribution of the supported object. The alignment is essential to ensuring that the device can handle the expected load. Misalignment may result in ineffective support or damage to the hydraulic rods. Hence, it’s vital to align the installation with the centerline of the supported equipment to ensure stable operation and avoid performance degradation.
3. Functional Installation Timing
Gas springs act as functional supports, distinct from conventional mechanical components. Proper installation at the right moment is key to fulfilling their role. Misinstallation or delays may hinder their ability to provide effective support. Gas springs are often used in specialized environments, such as automotive, textile, and printing machinery. Due to their lightweight structure, smooth operation, ease of use, and affordability, gas springs are highly preferred in these industries.
They are also versatile, functioning well in extreme conditions such as high-altitude areas, acidic or alkaline environments, and extreme temperatures.
4. Preservation of the Sealing Mechanism
The gas spring’s internal pressure is maintained by its sealed construction, which must not be tampered with or damaged. It’s crucial to avoid subjecting the gas spring to extreme heat or physical damage, as this could compromise its internal structure. Since gas springs contain high-pressure gas, modifications to the equipment while the rod is in place can be dangerous and are strongly discouraged.
5. Optimal Operating Temperature and Environmental Conditions
Gas springs function best within a temperature range of -36°C to 72°C. Operating outside of this range may impair performance or damage the spring. Due to their specific operational needs, gas springs are suitable for both standard and extreme environments, such as high-altitude, acidic, or alkaline conditions. This makes them highly adaptable to various industries, including automotive, engineering, and textile machinery, among others.
6. Utilization of Spherical Mounting Heads for Enhanced Flexibility
In certain applications, spherical heads are recommended for use due to their ability to rotate freely. This feature provides greater flexibility and precision in motion, ensuring that the gas spring can adjust to various angles and positions without loss of performance. The use of spherical heads improves the responsiveness and adaptability of the gas spring in complex mechanical systems.
7. Material Considerations for Different Applications
Gas springs are manufactured using different materials based on their intended application. Common materials include standard steel and stainless steel. Standard gas springs are frequently used in everyday products such as adjustable chairs and gas-lift beds. On the other hand, stainless steel gas springs are more suitable for specialized industries, such as food processing, medical devices, military equipment, and high-temperature environments, where corrosion resistance and durability are critical.
Conclusion
To ensure the efficient operation of gas springs in industrial applications, it is important to adhere to installation best practices, maintain a suitable working environment, and choose the appropriate materials based on specific use cases. By understanding these technical requirements, industries can leverage the full potential of gas springs, ensuring longevity, safety, and optimal performance in a wide range of applications.