When assessing the quality of a gas spring, several critical factors must be considered. These aspects directly impact the performance, reliability, and lifespan of the gas spring. Below is a detailed breakdown of these factors:
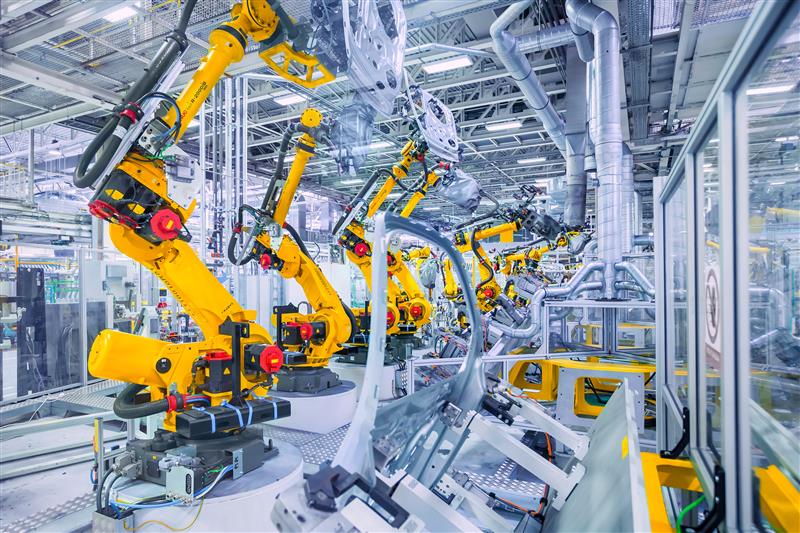
1. Sealing Performance
The most fundamental aspect of a gas spring is its sealing performance. A well-designed gas spring must maintain proper sealing to prevent any leakage of oil or gas. Poor sealing will lead to malfunction and can severely reduce the product’s effectiveness. Over time, this could result in pressure loss and cause the gas spring to fail, leading to mechanical issues in the application.
2. Force Accuracy
Accuracy in the force output is essential for the functionality of a gas spring. For instance, if a gas spring is designed to provide 500N of force, some manufacturers may achieve a high level of precision with deviations of no more than 2N. In contrast, others may produce gas springs with significant force discrepancies. Accurate force output is especially critical in applications requiring precise control and balance, such as in automotive, aerospace, or medical equipment.
3. Lifespan and Durability
The lifespan of a gas spring is determined by the number of complete cycles (extensions and compressions) it can perform. High-quality gas springs are engineered to withstand a high number of cycles, ensuring long-term functionality. The durability of the gas spring is a key performance indicator, particularly in industries where continuous and repeated use is expected.
4. Force Variation During Stroke
Ideally, a gas spring should provide a consistent force throughout its entire stroke. However, due to design and manufacturing variations, it is common for the force to fluctuate during movement. The degree of this variation is a critical measure of quality—gas springs with minimal force variation during operation are considered superior. A large fluctuation in force can indicate poor design or inferior manufacturing, which may lead to inconsistent performance and early wear.
5. Factors Impacting Longevity
To maximize the lifespan of a gas spring, certain precautions should be taken during its use. Regular maintenance, avoiding overloading, and operating within the recommended temperature and environmental conditions can significantly extend the service life. Ensuring the gas spring is not exposed to contaminants such as dust or corrosive substances can also prevent premature degradation.
Additional Considerations
For specific applications, gas springs can be designed with enhanced features, such as:
- Corrosion-resistant materials for use in harsh environments.
- Temperature tolerance adjustments, allowing for reliable performance in extreme heat or cold.
- Customizable force settings to suit specialized machinery or equipment.
By focusing on these key aspects—sealing performance, accuracy, lifespan, and force consistency—manufacturers can ensure that their gas springs meet the rigorous demands of modern engineering and industrial applications.