When designing and installing gas springs in automotive tailgates, several key factors must be carefully analyzed to ensure optimal functionality and durability. This document outlines the primary considerations in the installation and design process, providing technical details and product insights.
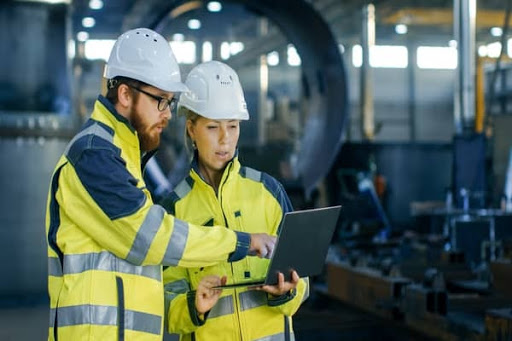
1. Confirm the Hinge Axis Location of the Tailgate
Before starting the installation of a gas spring in an automotive tailgate, it is crucial to validate the previously collected data. The following checks should be made:
- Ensure the two hinges of the tailgate are coaxial. This ensures smooth movement during the tailgate’s opening and closing processes.
- Check for any potential interference between the tailgate and surrounding body panels throughout its range of motion.
- Confirm that there is sufficient space allocated for the installation of the gas spring within the tailgate assembly. This includes room for both the gas spring itself and its range of movement when in operation.
2. Determine the Total Mass and Center of Gravity of the Tailgate
The mass of the tailgate is the combined weight of several metal and non-metal components, such as:
- Tailgate metal sheets
- Tailgate glass
- Rear wiper systems
- License plate lights and decorative panels
- License plate
- Tailgate locks and interior trim panels
With the densities of these materials known, software such as CATIA can be used to calculate both the total weight and the center of gravity (CG) coordinates of the tailgate. The CG location is essential for determining the placement and force requirements of the gas spring.
3. Identify the Gas Spring Installation Points
The installation points for the gas spring, in theory, refer to the ball joint rotation centers on both ends of the gas spring. Typically, the gas spring is mounted with the piston at the top and the piston rod at the bottom.
Key considerations for gas spring installation:
- The gas spring must be connected to the tailgate’s inner panel using a bracket. This bracket must allow clearance for the outer diameter of the piston and provide sufficient room for the piston’s movement.
- A reinforced nut plate must be installed inside the tailgate to secure the gas spring bracket. Both the nut plate and the bracket must meet the strength and stiffness requirements of the gas spring, especially under maximum load conditions.
- The upper installation point of the gas spring (on the bracket) significantly affects the required supporting force of the gas spring. Reducing the distance between this point and the hinge axis by 10% can increase the gas spring’s support force by more than 10%, while also impacting the stroke length. The design objective is to minimize the support force needed, as overly high forces can increase manufacturing costs and impose higher stiffness requirements on the tailgate structure.
4. Determine the Tailgate Opening Angle
The tailgate’s opening angle is determined based on ergonomic analysis. Although there are no strict regulations on the height of the lower edge of the tailgate when fully open, user comfort must be prioritized.
- The recommended height for the lower edge of the fully open tailgate is around 1800 mm from the ground. This height strikes a balance between ensuring the user’s head does not hit the bottom of the tailgate and making the tailgate handle easily reachable.
- The opening angle will vary depending on the vehicle’s height and structure, typically ranging between 100° and 110° relative to the vertical plane.
- Additionally, the tailgate’s maximum opening angle must be less than the maximum angle that the hinge can accommodate. The gas spring must also include a buffer mechanism at the end of its stroke to prevent damage to components from abrupt stops.
5. Develop 3D Models and Design Connection Methods for the Gas Spring
Once the key parameters and the type of gas spring are determined, a 3D model of the gas spring should be developed. This model should include:
- The external dimensions of the gas spring
- The relationship between its stroke and motion
- The structure and movement of both ends, including the ball joints and bolts
The gas spring’s connection method will depend on the specific installation location and the specifications of the selected product from the supplier. Common connection methods include:
- Both ends of the gas spring mounted on brackets
- One end directly mounted to the vehicle body
Each method should be carefully selected based on the vehicle’s design requirements and the supplier’s recommendations.
Conclusion
By paying close attention to these key aspects—hinge axis alignment, tailgate mass, installation points, opening angles, and connection designs—engineers can ensure that the gas spring system is both effective and durable. The use of 3D modeling software allows for precise calculations, aiding in the selection of the right gas spring specifications and optimizing the overall design process. Proper attention to these details not only improves functionality but also reduces costs and potential failures in the final product.