Gas springs are highly effective components used in various industrial and commercial applications. However, their lifespan and performance can be severely affected by improper handling and storage. To ensure optimal function and durability, several precautions should be observed during the use, storage, and transportation of gas springs. Below are the primary factors that contribute to gas spring damage:
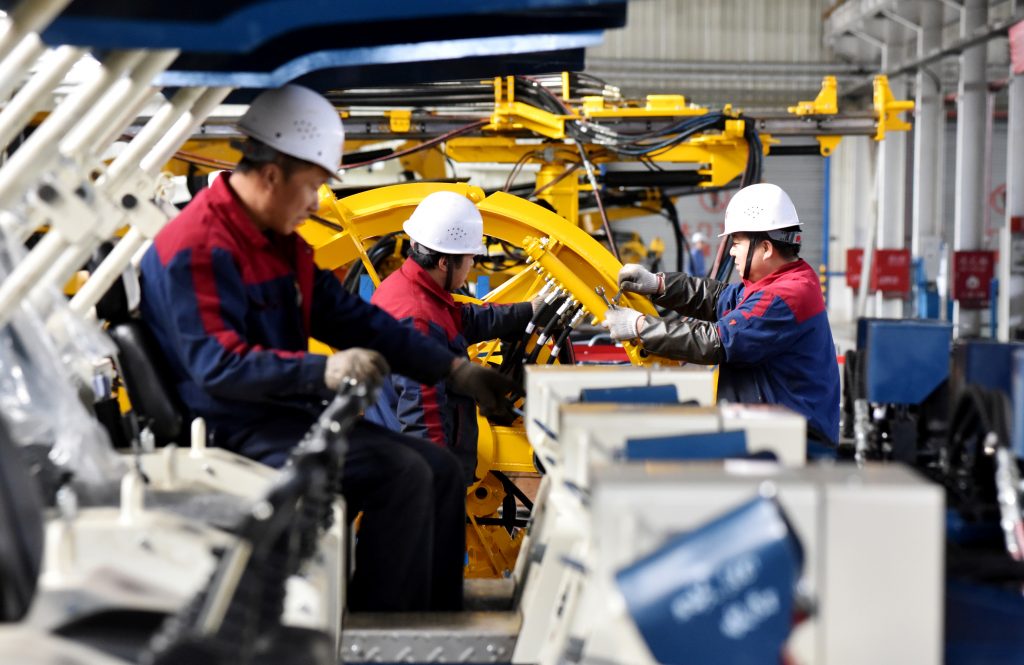
1. Avoid Modifications
Any form of reprocessing or modification of the gas spring is strictly prohibited. This includes altering its structure or attempting to adjust its internal components. Unauthorized alterations can compromise the integrity of the gas spring, leading to failure or malfunction.
2. Do Not Weld or Expose to Extreme Heat
Gas springs should never be subjected to welding or exposed to fire. High temperatures can cause deformation of the spring or even lead to an explosion due to the internal gas pressure. Always ensure that the gas spring is kept away from sources of extreme heat.
3. Store in Controlled Environments
Proper storage is critical for the longevity of gas springs. It is essential to keep them in a cool, dry place, away from direct sunlight, moisture, and dust. Excessive exposure to heat or humidity can cause corrosion or damage to the seals, resulting in leakage and a reduced operational lifespan.
4. Do Not Dismantle Components
Gas springs and their associated fittings, such as hoses or connectors, should never be disassembled or tampered with. Inappropriate handling of these parts, particularly under high pressure, can be extremely dangerous. The components may eject with force, posing a serious safety risk. Always consult a professional if maintenance or repairs are required.
5. Handle with Care During Transportation
During storage or transportation, gas springs should be handled carefully to avoid collisions, particularly between the gas springs themselves. Special care should be taken to prevent scratches or damage to the piston rod, as any surface imperfections can significantly shorten the lifespan of the gas spring. Proper packaging and cushioning should be used to protect the components from impact.
Additional Technical Considerations
Internal Pressure Management: Gas springs rely on precise internal gas pressure for optimal performance. Any imbalance or loss of pressure due to improper handling or environmental factors can result in erratic behavior or failure.
Seal Integrity: The seals within a gas spring are critical in maintaining the internal pressure and preventing gas or fluid leaks. Exposure to harsh environmental conditions, such as extreme temperatures or corrosive materials, can degrade these seals over time, leading to reduced effectiveness or total failure.
Material Compatibility: When selecting a gas spring for specific applications, it is essential to consider the material compatibility. Some gas springs are coated or treated to resist corrosion or wear in challenging environments. Using an incompatible spring for a particular application can result in premature wear or damage.
By following these guidelines and maintaining a strict adherence to proper handling procedures, the lifespan and performance of gas springs can be maximized, ensuring safe and efficient operation in their intended applications.