Stainless steel gas springs are widely used in various industries due to their excellent mechanical properties, resistance to corrosion, and adaptability to different environmental conditions. This document provides an in-depth analysis of the materials commonly used in the production of stainless steel gas springs, focusing on the properties, performance, and manufacturing options available for different grades of stainless steel.
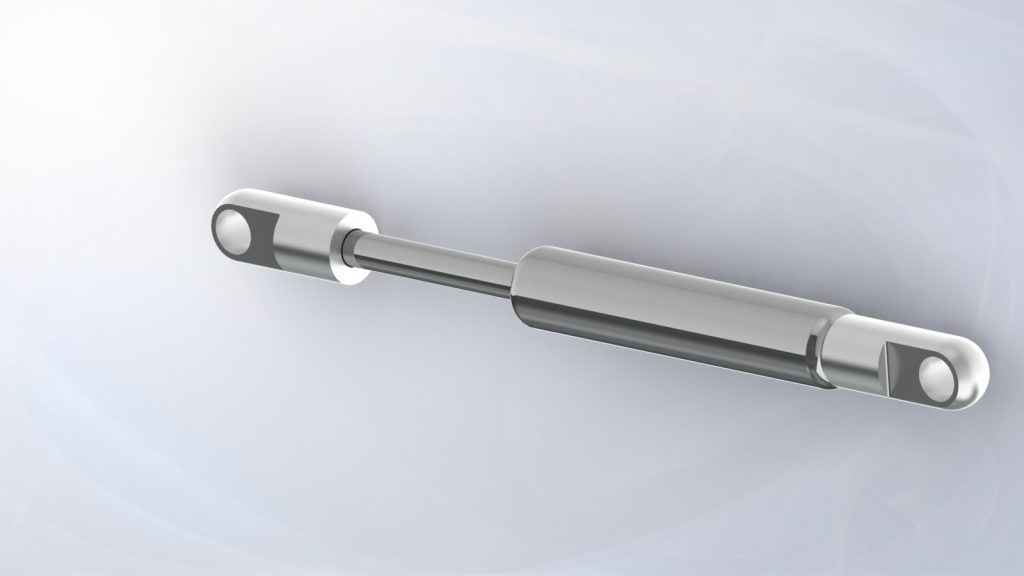
Common Materials Used in Stainless Steel Gas Springs
The most commonly used materials for manufacturing stainless steel gas springs include various grades of stainless steel, such as 304, 302, 301, 316, 316L, 321, 202, 201, 430, and 420. Among these, 304 and 302 stainless steels are the most popular due to their excellent balance of mechanical performance, corrosion resistance, and cost-effectiveness. These materials are also highly versatile, making them suitable for a wide range of applications, from industrial machinery to consumer products.
Key Features of 302/304 Stainless Steel
- Uniform and Aesthetic Surface Finish:
Both T302 and T304 stainless steels are known for their aesthetically pleasing, uniform surface finish. This characteristic makes them ideal for applications where appearance is important, such as in consumer-facing products or precision instruments.
- Good Formability and Elasticity:
These materials offer excellent formability, meaning they can be easily shaped or molded during the manufacturing process without losing their mechanical properties. Additionally, they provide uniform elasticity, making them highly suitable for gas springs, which rely on consistent force and movement.
- High Plasticity and Fatigue Resistance:
T302 and T304 stainless steels exhibit high plasticity, which allows them to withstand deformation without breaking. This property, combined with high fatigue resistance, ensures that gas springs made from these materials can endure repeated cycles of compression and extension without experiencing failure.
- Corrosion and Heat Resistance:
One of the most critical features of T302 and T304 is their excellent resistance to corrosion and heat. These materials can perform well in a wide range of temperatures and environmental conditions, making them suitable for both indoor and outdoor applications. Their ability to resist rust and chemical damage extends the lifespan of gas springs, reducing maintenance costs and ensuring reliable performance.
- Surface Finishing Options:
The surface state of stainless steel gas springs can be customized according to the needs of the customer. Options include bare wire, nickel-plated spring wire, and resin-coated spring wire. Additionally, stainless steel gas springs can be supplied in various finishes, such as bright, matte, or semi-bright finishes. Customers can choose the appropriate surface finish based on the precision and aesthetic requirements of their product.
- Magnetic Properties:
Stainless steel gas springs can be made with either non-magnetic or weakly magnetic properties, depending on the specific alloy and processing methods used. This feature is particularly useful in sensitive electronic environments or applications where magnetic interference needs to be minimized.
- Applications and Performance
Stainless steel gas springs are designed for a wide range of applications, including automotive, aerospace, industrial machinery, medical equipment, and consumer products. Their superior mechanical properties, combined with the ability to customize surface finishes and magnetic properties, make them ideal for both precision engineering and heavy-duty industrial use.
Gas springs made from 304 and 302 stainless steel are especially favored in industries requiring corrosion-resistant materials that can operate in harsh environments, such as marine equipment or outdoor machinery. Additionally, their heat resistance makes them suitable for high-temperature applications, including engines and manufacturing processes that involve heat exposure.
Conclusion
Stainless steel gas springs offer a combination of mechanical strength, corrosion resistance, and customizable features that make them a versatile and reliable choice for a broad spectrum of industries. By selecting the appropriate stainless steel grade and surface finish, manufacturers can optimize the performance and aesthetics of their gas springs to meet specific application needs. The use of T302 and T304 stainless steels, in particular, ensures that these gas springs can withstand demanding operational conditions while providing long-term durability.